Commercial Roofing – Massachusetts
Location: Massachusetts
Property Type: Large-Scale Manufacturing Facility
Project Date: September 2017 (Duration: 2 Months)
Product Used: White Reinforced .060 Poly-Vinyl Chloride (PVC) Roofing Membrane, Polyisocyanurate Insulation, Bristolite Skylights
Reason: Aging Roof
Project Summary
This extensive, multi-roof commercial project delivered complete replacement and rehabilitation across four separate roofing sections at a major manufacturing facility in Massachusetts. The 120,000-square-foot area had undergone several expansions over the years, but had avoided replacement. The facility’s roofing system reached the end of its lifecycle, making it clear that it was time for a full replacement in order to maintain the building’s integrity and business operations.
Our team at Vanguard Roofing implemented a carefully phased renovation strategy that corrected deteriorating conditions while maintaining the facility’s full operational capacity throughout the construction period. By applying advanced materials and specialized installation techniques, we transformed the facility’s roofing infrastructure into a high-performance system built to withstand harsh New England weather conditions while boosting energy efficiency and interior comfort.
The Challenge
The manufacturing facility presented multiple complex challenges that required careful planning and specialized expertise. Years of exposure to extreme weather conditions, coupled with outdated materials and installation methods, had left the roof vulnerable to failure at multiple points. Our team needed to develop solutions to address both immediate concerns and long-term performance requirements.
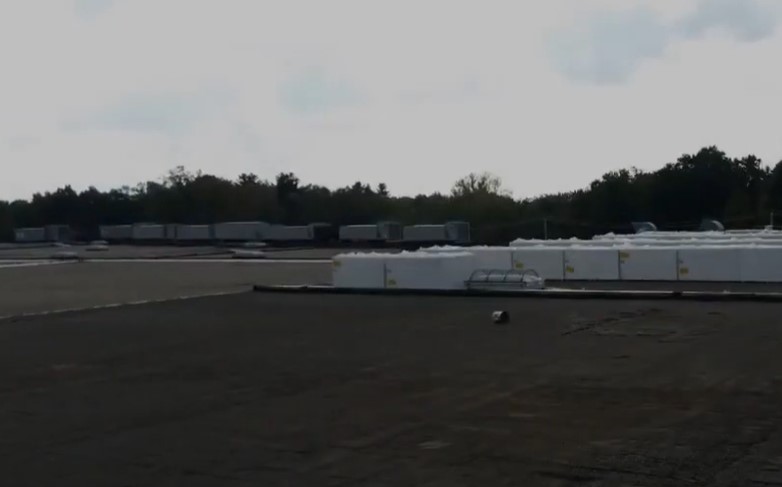
Roof 1 Challenges:
- Deteriorated built-up roofing with extensive ponding water
- Compromised metal edge details create entry points for moisture
- Heavy aggregate requiring specialized removal equipment
- Deck damage requiring assessment and targeted replacement
Roof 2 Challenges:
- Outdated skylights with compromised seals cause light transmission issues
- Insufficient insulation contributes to excessive energy costs
- Complex HVAC and pipe penetration details requiring custom solutions
- High visibility area requiring minimal disruption to operations below
Roof 3 Challenges:
- Hidden moisture issues within existing insulation layers
- 10’ x 200’ area of the severely damaged substrate along the rear building section
- Existing expansion joints failing to accommodate building movement
- Need for high wind-resistant edge details due to location exposure
Roof 4 Challenges:
- Extensive debris and aggregate requiring thorough cleaning
- Multiple saturated insulation areas detected through diagnostic testing
- Inadequate drainage causes standing water and membrane degradation
- Complex integration with adjacent roofing systems
Additionally, each roof section presented common challenges:
- Working at heights with heavy materials presented significant safety risks
- Maintaining the integrity of surrounding roof areas during renovation
- Coordinating efficient debris removal and multiple work teams
- Installing specialized high-performance materials with precision
- Managing space constraints for equipment without disrupting facility operations
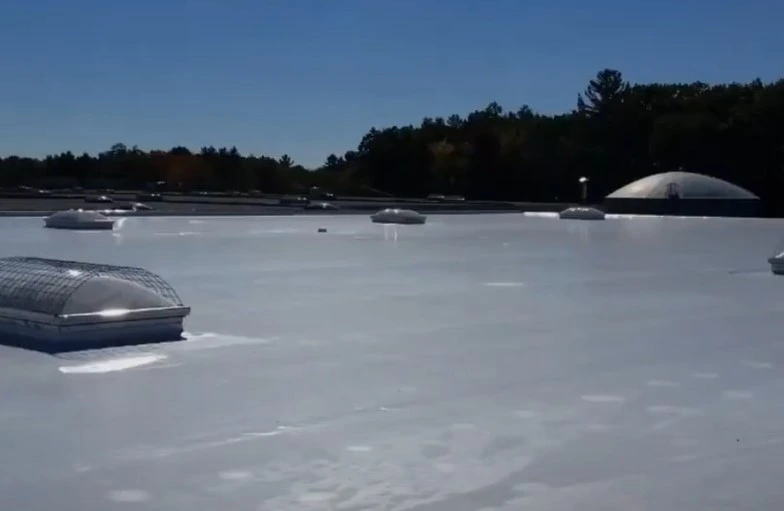
Our Solution
After a thorough assessment, we developed a multi-phase implementation plan that strategically targeted each roof section with customized solutions based on specific condition assessments. Our approach allowed us to address both immediate concerns and long-term performance goals while minimizing disruption to daily operations.
Roof 1 Solution:
We performed a complete rip and removal of all loose aggregate, dust, and debris using heavy-duty street brooms and roof vacuum machines. Our team dismantled the existing built-up roofing assembly, insulation, and metal edge details to expose the underlying deck, then replaced compromised sections with new metal decking. We installed a white reinforced .060 PVC roofing membrane using the specialized RhinoBond Attachment Method over newly installed insulation, creating a monolithic roof system through heat welding.
Roof 2 Solution:
Our team installed two layers of polyisocyanurate insulation totaling R-30 thickness across the entire roof field. We applied a white reinforced .060 PVC roofing membrane using the RhinoBond Attachment Method with heat welding for a watertight system. The project included the removal of existing skylight lenses, frames, and security screens, replacing them with new Bristolite Skylights featuring thermally broken frames with clear-over-white prismatic domes and mill finish aluminum frames. We added new 18” curbs and integrated safety screens while meticulously installing flashing details at HVAC curbs and pipe penetrations.
Roof 3 Solution:
We conducted infrared scanning to identify saturated insulation areas, removing and replacing all compromised materials. After replacing damaged metal decking with new steel matching the existing profile, we focused on a critical 10’ x 200’ area along the rear of the building, exposing the deck and installing infill insulation with fasteners. The new system included a 3″ polyisocyanurate insulation assembly and white reinforced .060 PVC roofing membrane with expansion joint systems and high wind-compliant edge metal detailing.
Roof 4 Solution:
This area required sweeping and vacuuming all loose aggregate, dust, and debris from the roof surface. After performing an infrared scan to identify areas requiring insulation replacement, we removed compromised materials and inspected and replaced damaged decking. The completed system included a new 3” polyisocyanurate insulation layer with white reinforced .060 PVC roofing membrane, proper flashing details, expansion joints, and integrated drain assemblies.
Materials Used
The selection of materials for this project was critical to achieving both immediate performance requirements and long-term durability goals. Each component was chosen for its specific characteristics and compatibility with the overall design.
- White reinforced .060 Poly-Vinyl Chloride (PVC) roofing membrane
- Polyisocyanurate insulation (R-30 thickness)
- Bristolite Skylights with thermally broken frames
- Clear-over-white prismatic domes with mill-finish aluminum frames
- 18” skylight curbs with integrated safety screens
- Steel decking for compromised areas
- Specialized flashing materials for HVAC curbs and pipe penetrations
Highlights
The execution of this project showcased our team’s ability to overcome complex challenges while delivering exceptional results. The project’s most significant achievements stemmed from our ability to navigate logistical challenges. The manufacturing facility’s need for continuous operation required extraordinary coordination and safety measures beyond typical commercial roofing projects.
- Zero interruption to manufacturing operations throughout the entire two-month project duration, achieved through strategic phasing and after-hours work on critical areas
- Advanced diagnostic techniques, including electronic leak detection, to identify and address subsurface moisture issues prior to new system installation
- Specialized installation methods implementing robotic welding equipment for consistent seam quality across large membrane areas
- Coordinated material deliveries to accommodate limited staging areas without interrupting workflow
- Enhanced safety protocols exceeding industry standards, including temporary guardrail systems and designated safety monitors
Results & Benefits
The manufacturing facility now benefits from a completely rehabilitated roofing system that provides superior protection against the elements while contributing to improved operational efficiency. The integration of advanced materials and installation techniques has resulted in a roofing assembly that significantly outperforms the original system in all critical performance categories.
The new roofing system has delivered:
- Complete elimination of previous water intrusion issues through superior waterproofing and properly designed details at all penetrations and transitions
- Significant improvement in thermal performance with measurable reduction in heating and cooling costs during the first year of operation
- Enhanced natural lighting through modern skylight technology, reducing dependency on artificial lighting during daylight hours
- Extended roof service life with comprehensive 20-year warranty coverage, providing long-term protection and peace of mind
- Improved facility aesthetics with clean, professional finishes that enhance the property’s appearance and value
Special Features:
The execution of this project showcased our team’s ability to overcome complex challenges while delivering exceptional results. The project’s most significant achievements stemmed from our ability to navigate logistical challenges. The manufacturing facility’s need for continuous operation required extraordinary coordination and safety measures beyond typical commercial roofing projects.
- Zero interruption to manufacturing operations throughout the entire two-month project duration, achieved through strategic phasing and after-hours work on critical areas
- Advanced diagnostic techniques, including electronic leak detection, to identify and address subsurface moisture issues prior to new system installation
- Specialized installation methods implementing robotic welding equipment for consistent seam quality across large membrane areas
- Coordinated material deliveries to accommodate limited staging areas without interrupting workflow
- Enhanced safety protocols exceeding industry standards, including temporary guardrail systems and designated safety monitors